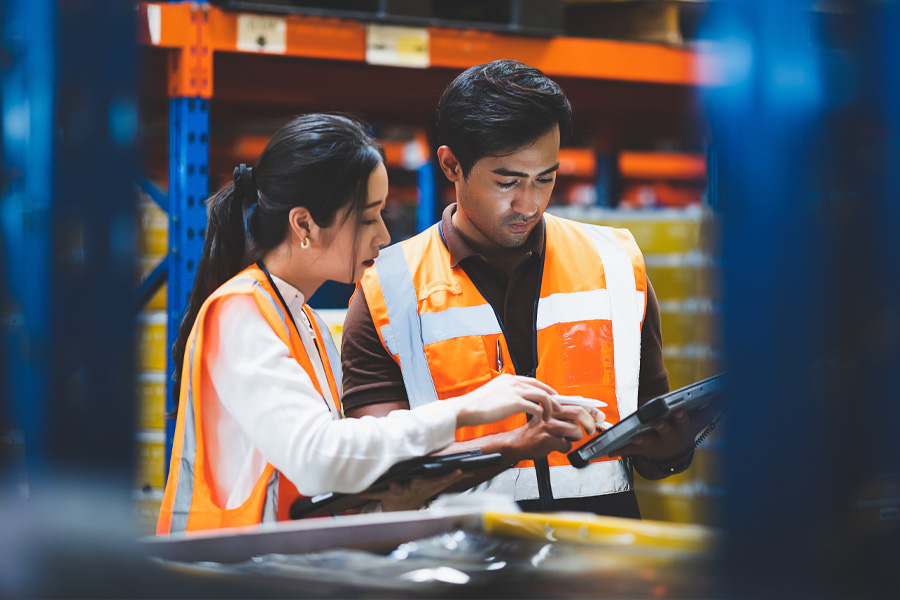
Observations: The most undervalued tool in your warehouse or distribution center
Just watching frontline employees at work can be the key to significantly increasing performance—if you do it right. While we’ve seen a number of companies using observations in warehouse or distribution center settings, they’ve typically done so in a very narrow, limited way; for example, they may limit their efforts to observing and coaching low-performing employees. It’s kind of like managing a sports team but only coaching the weak players, and coaching all of them the same way. That’s not going to win anybody any championships on the field, and it’s not going to do you much good in the warehouse or distribution center, either.
In my experience, a program that consistently observes all the workers who are picking and packing products—even the ones you think don’t need it—will pay off in higher worker performance, which in turn pays off in overall higher performance for the building. Here’s a great example. A colleague and I were visiting a distribution center where the manager told us about one stellar employee who performed at 130% day in and day out. But observing him at work in the context of the building’s established SOP showed he did not adhere to the requirement for level-picking. He was saving time and overperforming by skipping that step—but in the process, he was putting merchandise at risk for damage or loss, and making the next picker reach for their picks.
On the other hand, observations that engage all employees can provide useful guidance to them, and making changes based on their feedback can deliver significant improvements in overall building performance. We’ve seen improvements of up to 12%, compared to modest performance improvements of 1-2% for buildings that use observations in a more limited way.
So why are so many operators of distribution centers and warehouses not using observations to improve performance? A simple lack of awareness and challenges with scaling a program are probably to blame. A well-designed, scalable, technology-driven program for observing, supporting, and coaching workers, will enable them to reap the performance benefits that previously seemed beyond their reach.
Our company operates in more than 200 buildings, and the results we’ve seen and data we’ve collected lead me to truly believe that observations are one of the most undervalued tools available for operations leaders to achieve meaningful performance improvements. Next time, I’ll dig a little deeper into how to create a great observation.
Share: